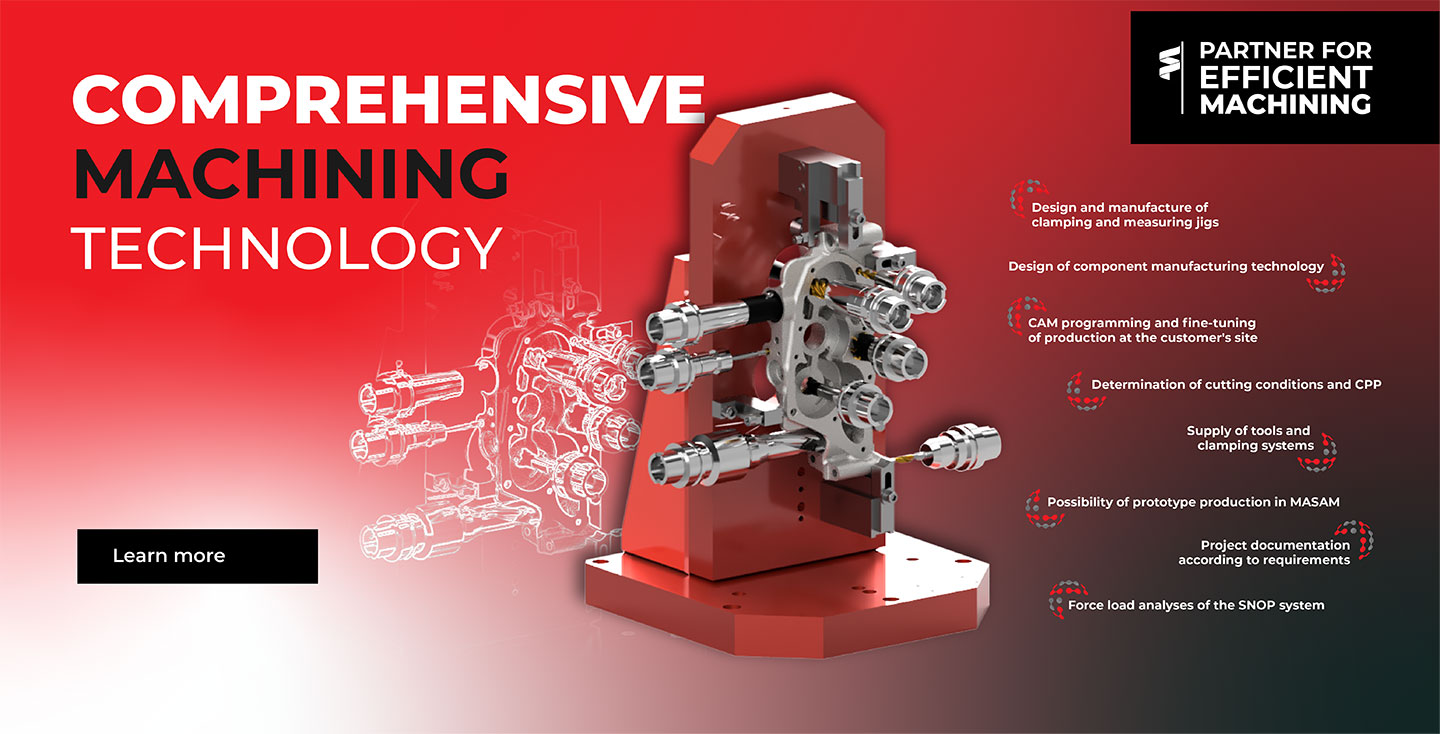
DISCOVER COMPLEXITY
AND SIMPLIFY YOUR WORK
Comprehensive machining technology from our company represents the entire
portfolio of services and products that customers can choose from in the form of various options.

Cost
We will design and manufacture independently the fixture for your project to reduce your procurement costs.

Time
We will save you time in the manufacturing process as we will also provide complete machining of the new product.

Durability
Our cutting tools are specially manufactured with high demands on their durability.

Cost
We will design and manufacture independently the fixture for your project to reduce your procurement costs.

Time
We will save you time in the manufacturing process as we will also provide complete machining of the new product.

Durability
Our cutting tools are specially manufactured with high demands on their durability.
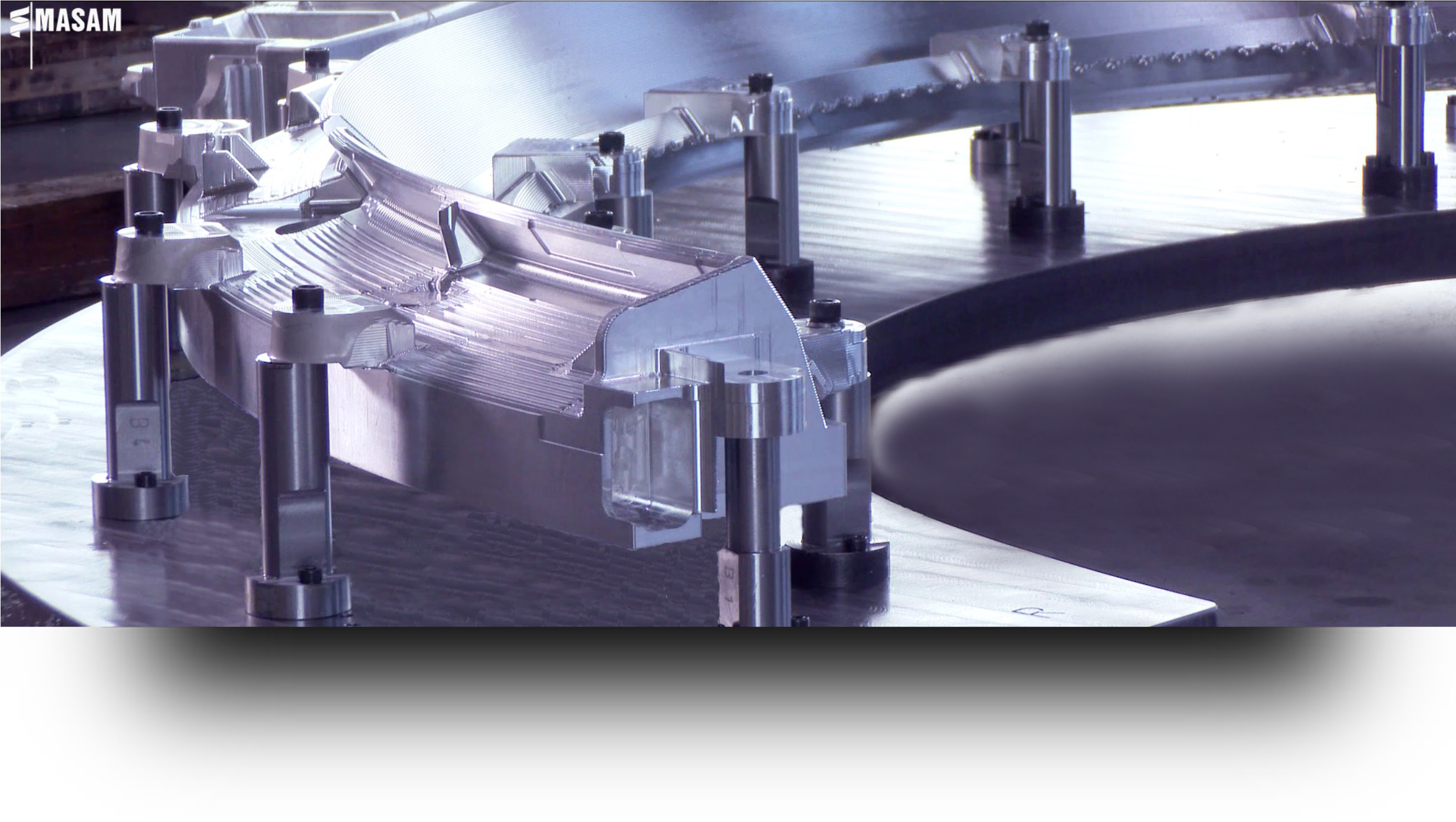
Production, measurement and assembly of preparations takes place directly in our MASAM production premises.
Standard part of the
supply of cutting tools
and clamping systems.
supply of cutting tools
and clamping systems.
- We will prepare technological documentation for the customer.
- Complete depiction of machined surfaces for individual tools.
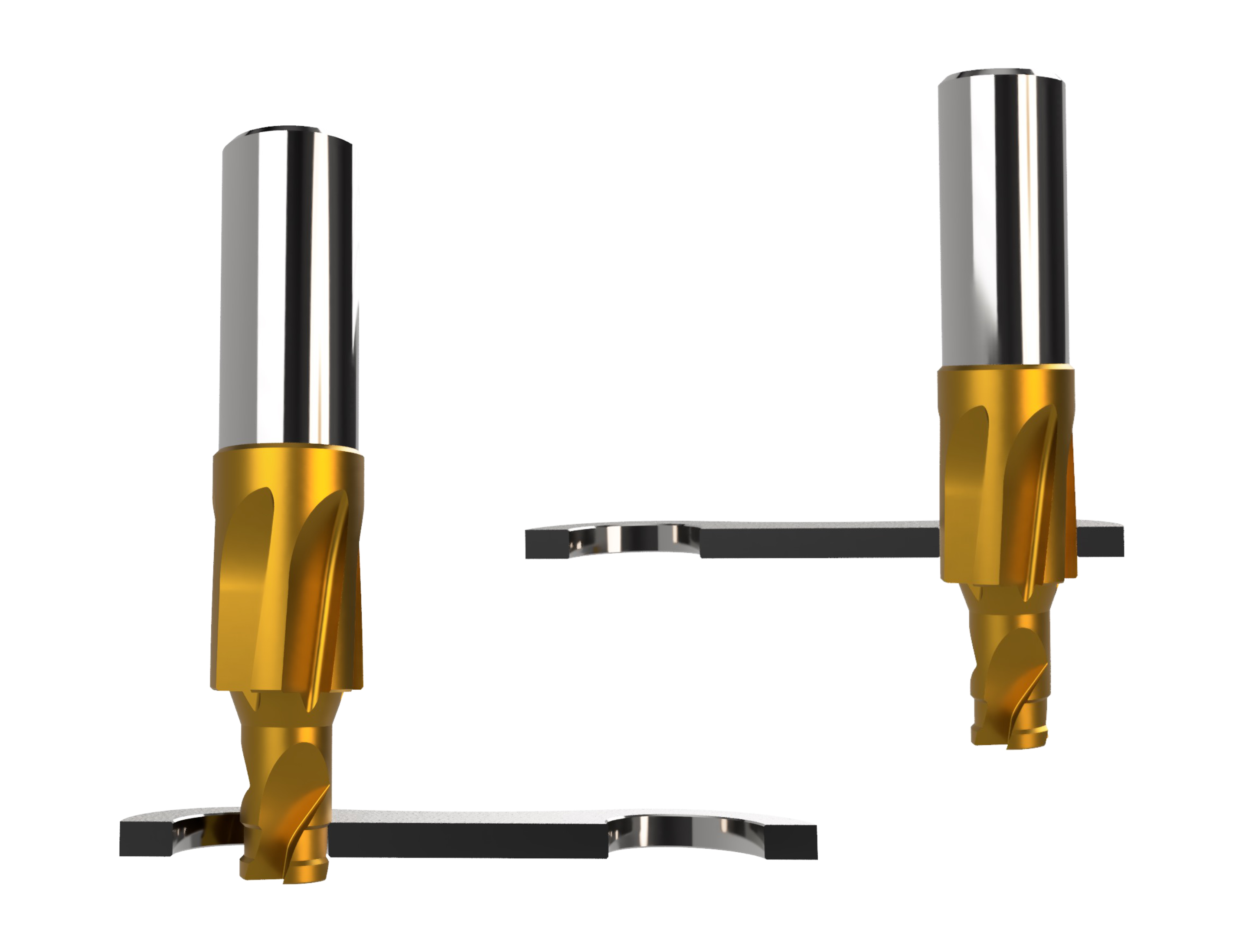
- Process simulation
We simulate for the customer the entire machining process of the part with total machining times as well as collision conditions.
- CL data
After agreeing on the production technology of the part in the form of simulation, we proceed to convert the CL data into an NC program.
- Production fine-tuning
Production fine-tuning at the customer’s site is ensured by the expedition of our application engineer and CNC programmer at an agreed time according to the customer’s capacity.
- The determination of cutting conditions is handled in the form of application sheets, which contain our recommended starting parameters as well as a range of maximum and minimum conditions.
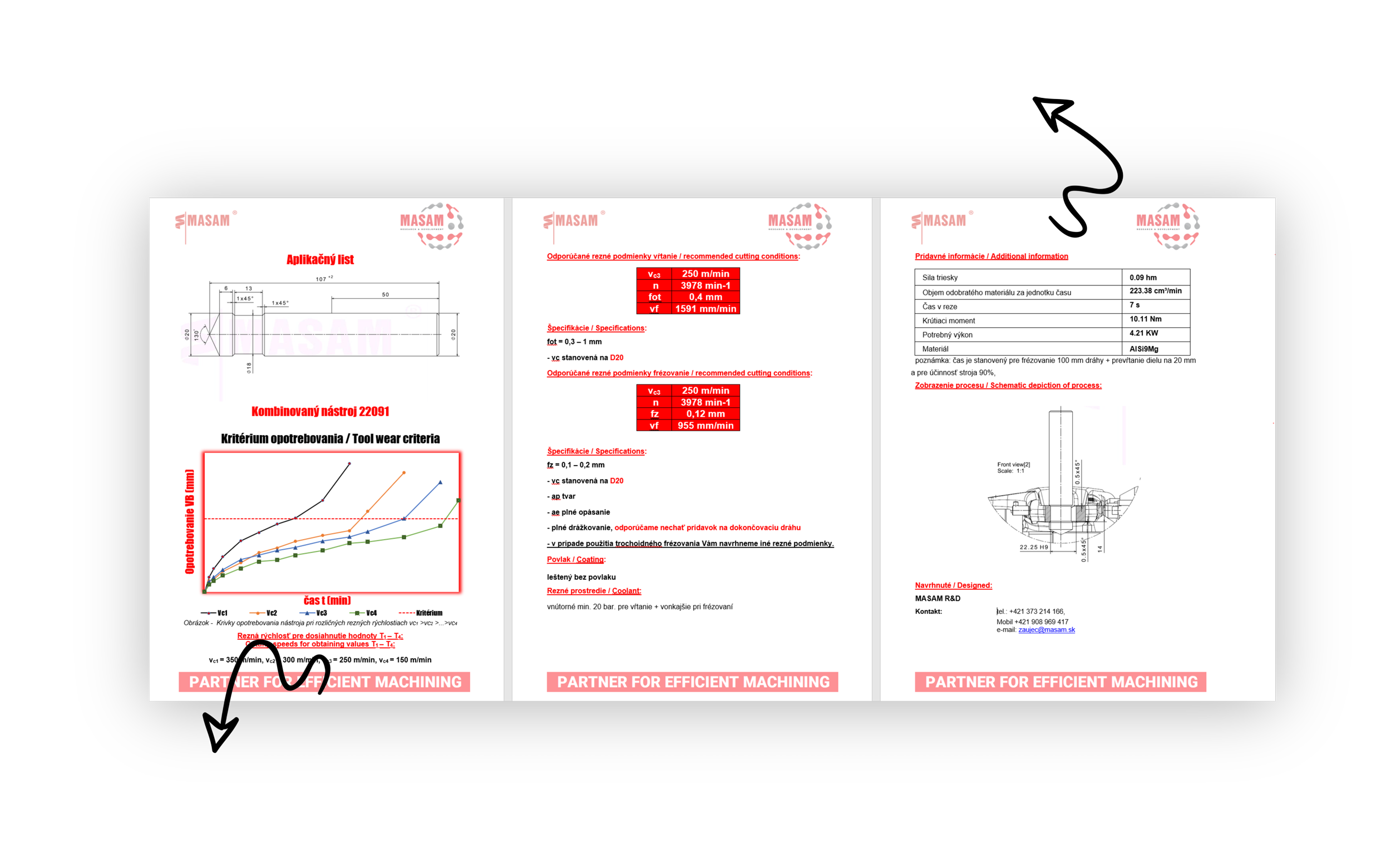
- Cutting forces, MRR, are also calculated for the recommended conditions. The application sheets also contain comments and notes on the machining process with the tool, as well as the estimated tool life.
- In determining the manufacturing cost per part, we work with each tool separately, the cost for its specific application, as well as the CPP cost overall. Alternatively, we provide the customer with all necessary machining times for a separate internal CPP analysis.
FIND OUT
HOW MUCH YOU CAN SAVE
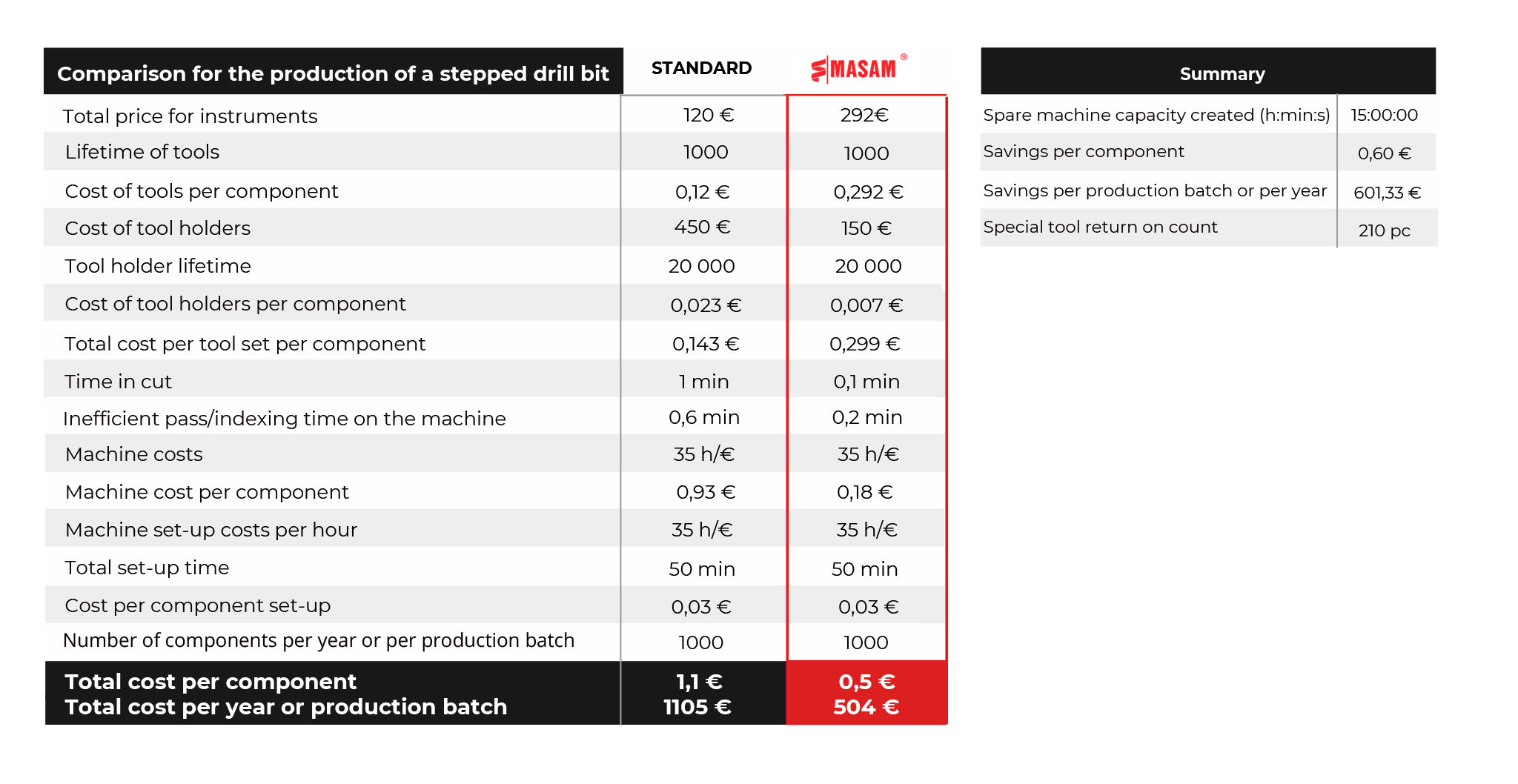
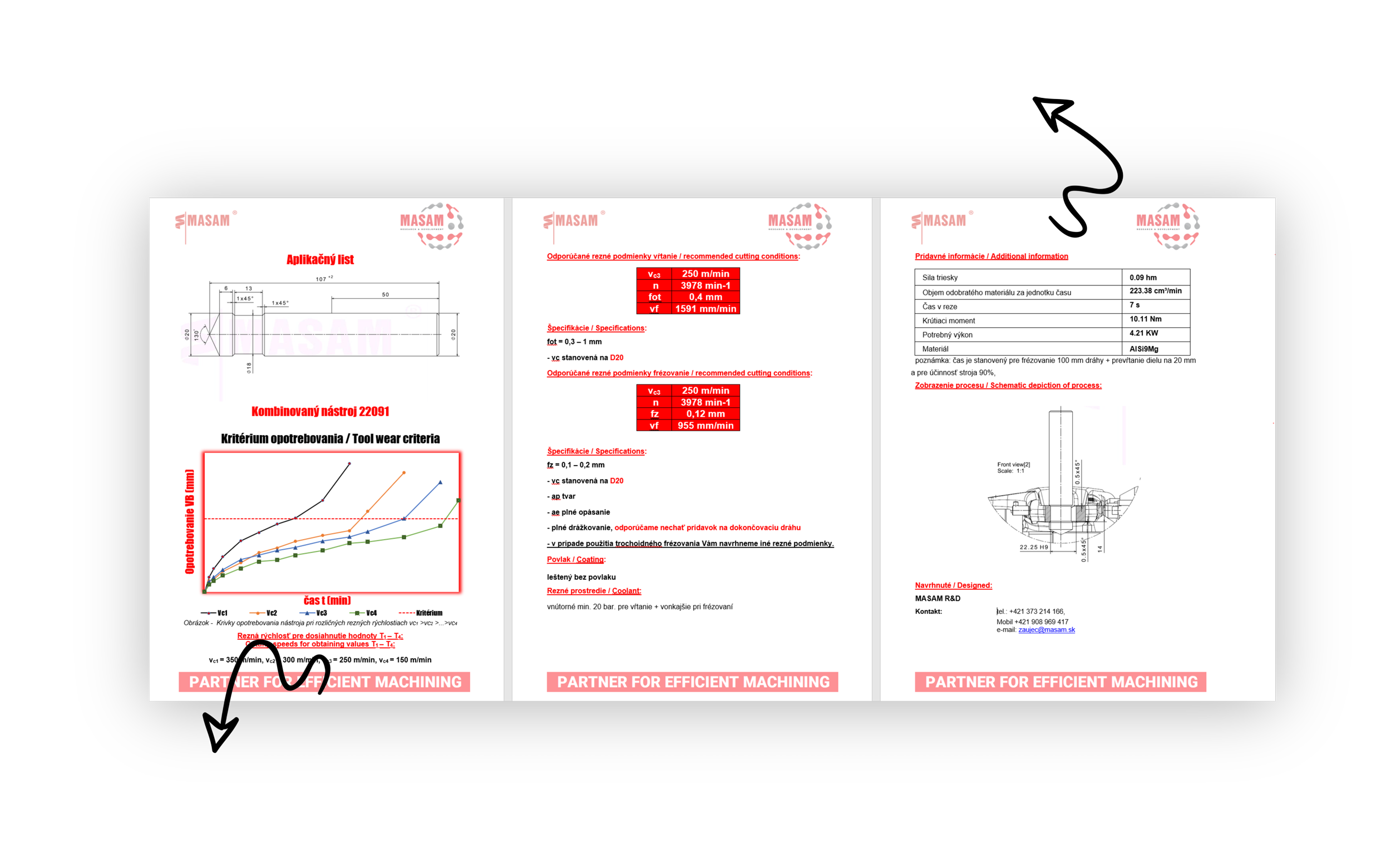
- The determination of cutting conditions is handled in the form of application sheets, which contain our recommended starting parameters as well as a range of maximum and minimum conditions.
- Cutting forces, MRR, are also calculated for the recommended conditions. The application sheets also contain comments and notes on the machining process with the tool, as well as the estimated tool life.
- In determining the manufacturing cost per part, we work with each tool separately, the cost for its specific application, as well as the CPP cost overall. Alternatively, we provide the customer with all necessary machining times for a separate internal CPP analysis.
FIND OUT
HOW MUCH YOU CAN SAVE
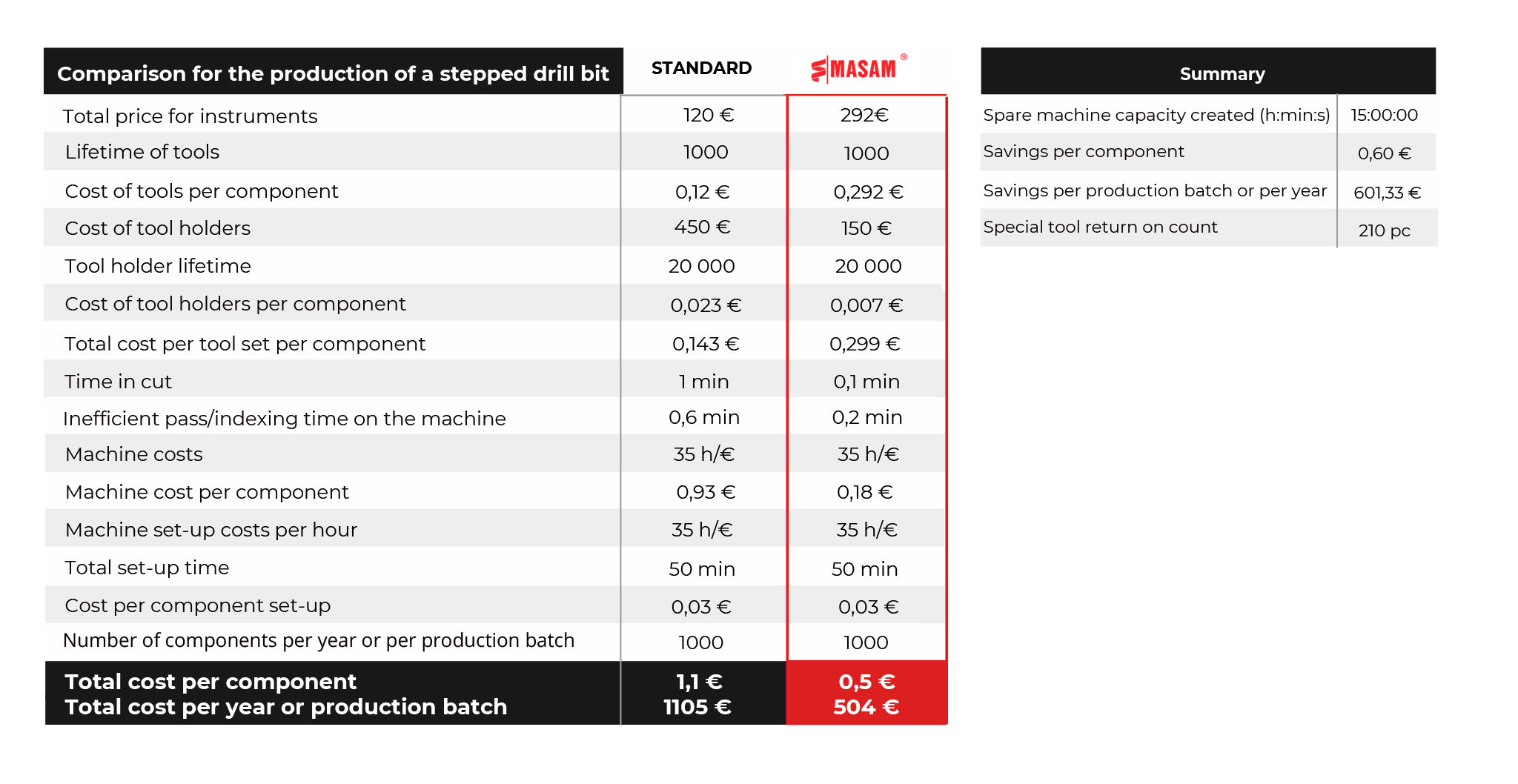
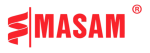
In addition to our own
standard and special VHM cutting
tools, we supplement our product
range with the official representation
of major manufacturers of cutting tools
and clamping systems.
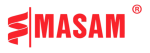
We also carry out initial
tooling of machine tools in this segment.
MASAM FMT tools are measured for special
and standard tools PKD, CBN.
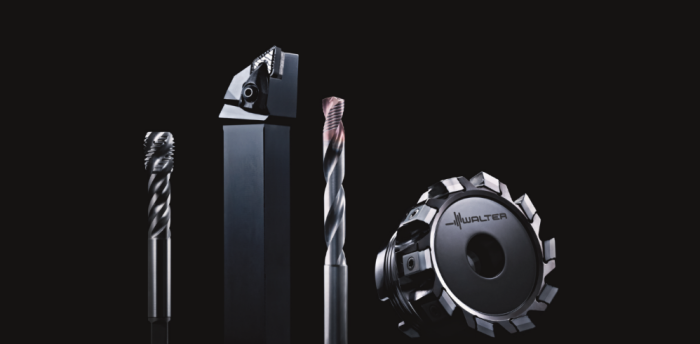
We supply tool clamping systems from leading companies
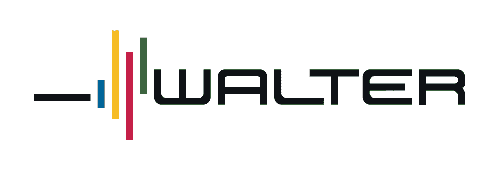
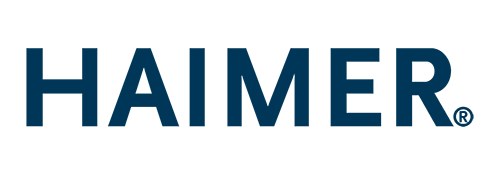
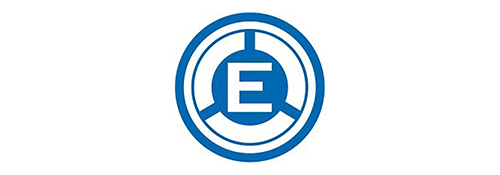
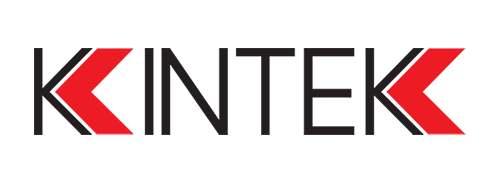
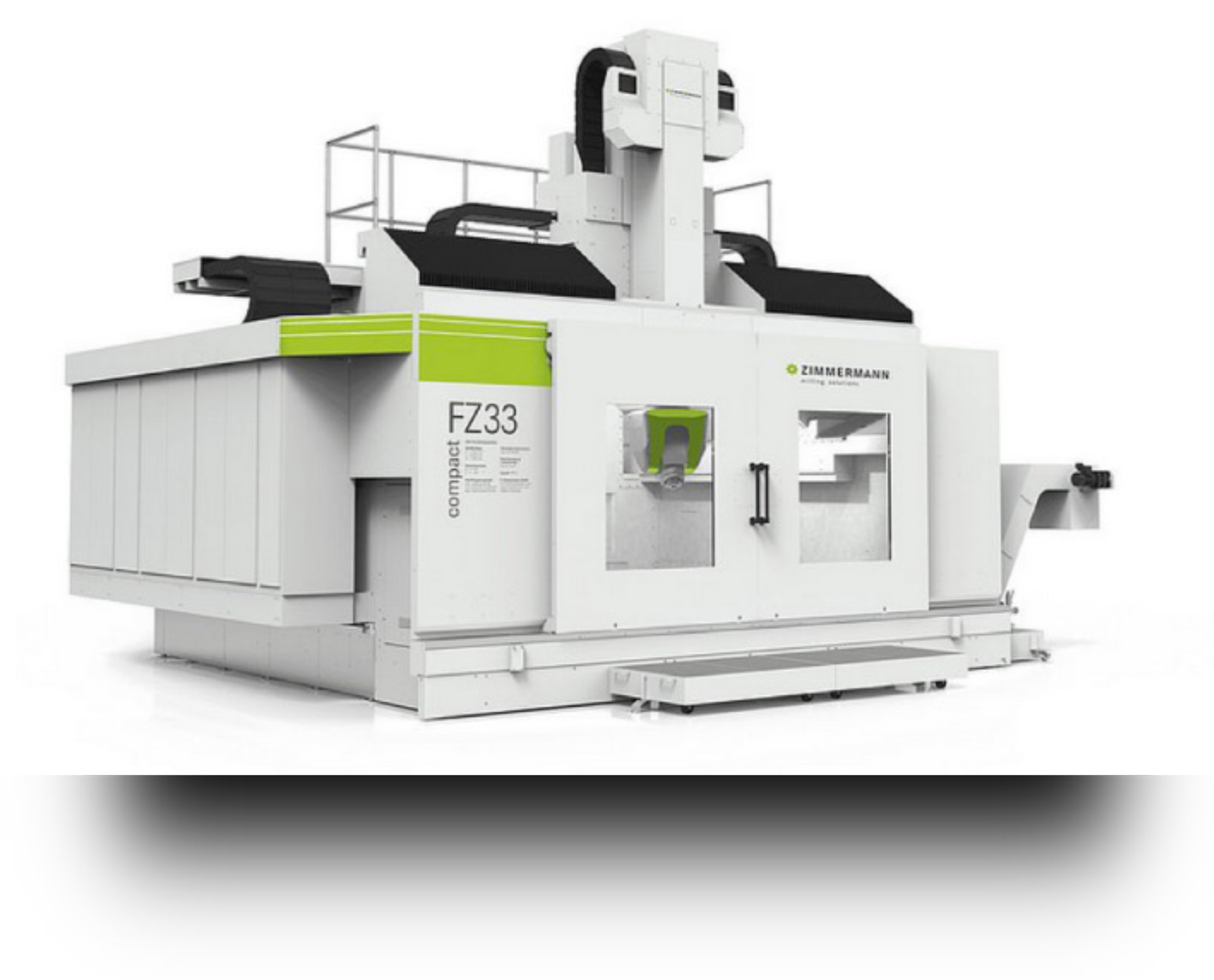
CLAMPING PROCEDURE
- Place and press the casting onto the bearing surfaces “D, E, F”.
- Consistently press the casting onto stop pins “A, B” and stop surface “C”.
- Tighten clamp “1” to a torque of 20 Nm.
- Tighten clamp “2” to a torque of 20 Nm.
- Tighten clamp “3” to a torque of 20 Nm.
- Tighten side stop “4” by hand without preload.
- Tighten side stop “5” by hand without preload.
- Visually check the casting for correct position.
- Tighten clamp “1” to a torque of 40 Nm.
- Tighten clamp “2” to a torque of 50 Nm.
- Tighten clamp “3” to a torque of 50 Nm.
- Tighten side stop “4” to a torque of 4 Nm and preload the corresponding lock nut.
- Tighten side stop “5” to a torque of 4 Nm and preload the corresponding lock nut.
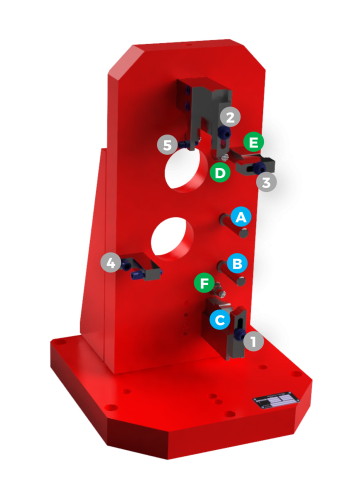
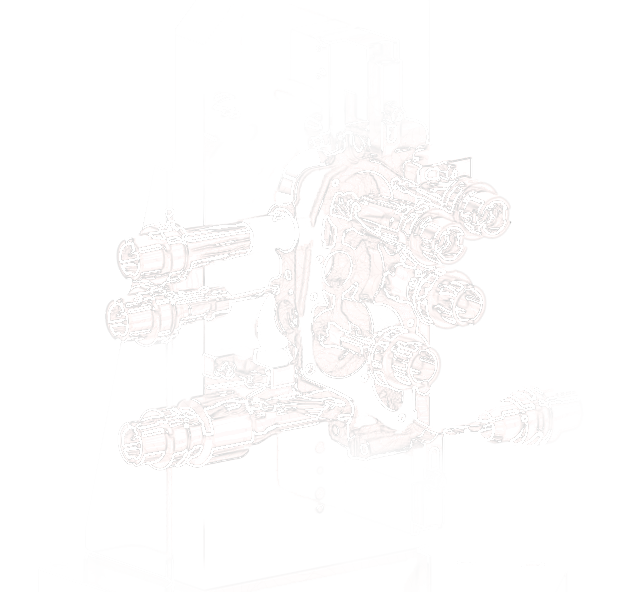
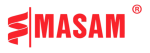
Provided service of calculation of cutting forces, force load
of the system, machine – tool –
workpiece – jig, falls within the comprehensive
turnkey technology solution.

The performance characteristics of the machine are a very important
parameter in the design of the machining technology.
In this respect, we try to match the individual machine operations
with the highest performance requirement to the performance
curves of the machine tool.
On the other hand, we always choose the workpiece clamping
so that with high clamping forces the workpiece is not
deformed and at the same time the machining process is stable.
GIVE US A TRY
TO MAKE YOUR PLANS AND VISIONS
BECOME A REALITY, YOU MUST HAVE THE COURAGE
AND CAPABLE PEOPLE.
HAS BOTH.
BECOME A REALITY, YOU MUST HAVE THE COURAGE
AND CAPABLE PEOPLE.
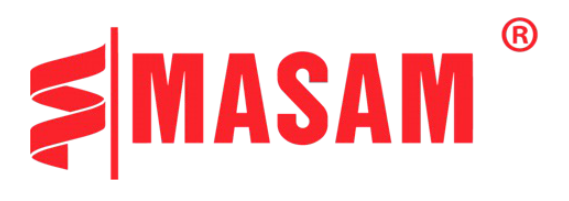